CBN, which stands for Cubic Boron Nitride, has revolutionized the machining sector ever since it’s invention. While you upgrade your conventional grinding wheels like vitrified Al2O3 or ceramic wheel to vitrified CBN, or vit-CBN, there are a few major points you should keep in mind.
Depending on your grinding machine, it might be made to handle both conventional as well as vitrified CBN wheels. But there are many cases where you need the addition of certain features so that the machine can run vit-CBN. Moreover, since the tuning and dressing is different for a CBN wheel from a conventional wheel, grinding and dressing conditions need adjustments.
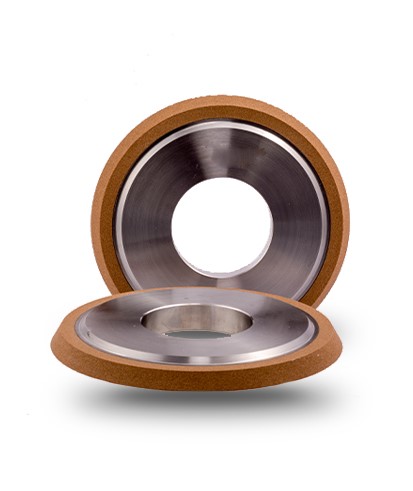
You might be wondering, “If I have to make so many adjustments in my process, why should I use CBN instead of Al2O3 or ceramic grains at all?” Do I have even a single reason to justify the shift? Well, I have 5. Here are the main advantages of CBN grinding over Aluminum oxide or ceramic grinding wheels.
Reasons to choose Vitrified CBN Grinding
1. Cycle Time
The ability to grind much faster than conventional abrasives is a reason our customers have started upgrading to CBN. Since its hardness is higher and its skip dress is higher, it can be pushed harder and cut quicker. This also eliminates machine down time due to less frequent dressing. So you save time on grinding as well as dressing.
2. Superhard Materials
New material such as M4 are becoming more popular. These materials resist abrasion and are hard to grind. It is more sensible to use CBN instead of conventional grinding wheels on such materials. Reason: If the harness of the alloy is close to the hardness of your Aluminum oxide or ceramic grinding wheel, it could glaze or damage the wheel.
3. Grinding Stock
If the total stock removal is high, it makes more sense to use a CBN Grinding wheel than a conventional one. Total stock removal can be high for three reasons. One, the number of parts is very high. Two, each part has a large amount of material to be peeled. And three, the part is asymmetric with some areas having considerable grinding stock.
4. Cost per Part / Operational Cost
CBN is a very hard material. Owing to its hardness, vitrified CBN cuts for longer and its wear rate is lower. A vit-CBN wheel reduces the amount of dressing and abrasive layer required to grind big batches. This can translate into lower overall operational costs.
5. Thermal Stability
The CBN grain has a higher thermal conductivity than Al2O3 or ceramic abrasive grains. This enables CBN to dissipate heat by conducting it away from the grinding zone. This in turn helps prevent any thermal damage or burning marks on the workpiece.
Points to remember before you upgrade
When switching from conventional grinding to a vit-CBN grinding process, it is important to review three principal areas:machine requirements, grinding wheel considerationsandoperator know-how.
A.Machine Requirements
Machine requirements involve the grinding wheel spindle, dressing system, the coolant system, machine rigidity and safety.
a. Wheel Spindle
The grinding wheel spindle needs rigid bearings to handle a heavier wheel. The core of the vit-CBN grinding wheels is usually made of steel. The CBN grinding wheels are very much heavier than conventional wheels because of this reason. The grinding or rotating speed (RPM) of the vitrified CBN wheels is also much higher and can go even above 120 mps (120m/sec).
In the recent years, plastic technology has made certain advances. This has led us to start using carbon fiber reinforced plastics (CFRPs) as a core material for vit-CBN wheels. This reduces the weight of the wheel tremendously. True, it will reduce the demand on your spindle. However, a cost-benefit analysis would be necessary to justify the price of the wheel.
b. Dressing System
Vit-CBN wheels require arotary dresseras opposed to a stationary dresser used in conventional grinding. Thus, the machines using conventional wheels typically do not include dressing spindles. In order to use a conventional machine for vitrified CBN wheels, it needs to be retrofitted with a dressing spindle and its attachments. The spindle shout be attached at a position which is rigid enough to take the dressing force.
c. Coolant System
When the grinding wheel is rotating at a very high speed, it tends to generate an air pressure which blows away the coolant. Therefore, the coolant flow for a vit-CBN wheel needs to be high considering the wheel speed. This means that the pump should provide enough pressure to ensure optimal delivery of coolant into the grinding zone. Some of our customers use specially designed nozzles which help break the air barrier and deliver coolant. Those nozzles also are designed to withstand coolant pressure.
In many cases, coolants used with conventional wheels can be used for vit-CBN. But it is recommended to work with the coolant manufacturer to come up with the best option, such as emulsion-type or oil-based coolant, as long as the overall process allows it.
d. Machine Rigidity
Because CBN is harder than any Al2O3 or ceramic grain, a grinding machine needs to be rigid enough to withstand the grinding forces. In addition to having tight spindles, close-fitting slides are necessary. Lack of stiffness can cause bending and vibration.
e. Safety
Use of safety guards on the machine is quintessential. Many machines using conventional wheels — particularly the older ones — don’t have the necessary guards and safety measures in place to keep the wheel or the workpiece particles from going airborne. When running vit-CBN at high speeds, it’s important to have a guard to protect the operator.
B.Grinding Wheel Considerations
If a cylindrical grinding machine is not able to spin the wheel fast enough, the vit-CBN specification will have to be modified for slower speeds. However, that will affect the performance and life of the wheel.
If a spindle cannot take the weight of the vit-CBN wheel, a smaller wheel will need to be designed, as long as the machine and process can accept that. In some cases, it may be possible to change the core of the wheel to a lighter material.
C.Operator Know-How
Handling a CBN wheel is different from handling a conventional wheel. The operator must be adequately trained in the proper way to handle a vit-CBN wheel. Besides being heavy, the vit-CBN wheel is also prone to rusting because of its steel core. Especially in a monsoon country like India. Therefore, the wheel should be stored in a dry area to avoid rust. Operators and engineers also are obligated to learn and determine the optimal conditions for grinding and dressing a vit-CBN wheel.
Vit-CBN wheels are a great option for production grinding due to their potential for increasing productivity and part quality and lowering tool costs. However, this is not a possibility for every application, so a thorough study should be conducted to determine the feasibility of such a project. You cancontact our teamto conduct the feasibility study with you as well as provide you with a suitable solution