How Our Expandable Reamers are Changing the Indian Hole Finishing Market
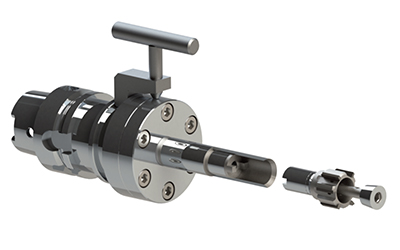
Hole making is one of the most common metalworking operations. In an earlier post, we showed you why reaming was better than fine boring. Especially for high volume hole finishing applications with tight dimensional tolerances and critical surface finish requirements. Here, you see how our Swiss-made expandable reamers are outperforming the most popular companies in this segment.
The tangible benefits
The below infographic very clearly portrays that our reamers, performed at the same machining parameters as our competitor (a popular international brand). But our reamer achieved double the life as compared to the competing European brand.
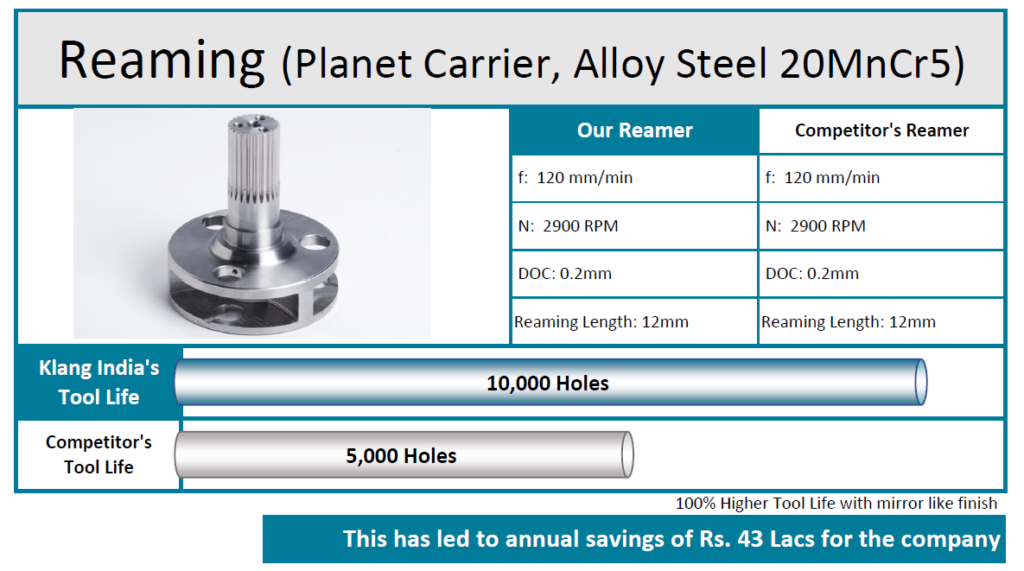
The intangible benefits
The above numbers only show the primary metrics of evaluating the process cost. However, the finish achieved with our reamer, which isn’t mentioned above, was a mirror finish in the first try.
Another indirect saving was the setup time wasted while setting up a reamer on a compensating type adopter. We replaced that with a hydro grip adopter for a round shank reamer. The result was a much better finish, phenomenal size control (attributed to Swiss-precision) and much lower setup time.
Before we began the trials, our deeply knowledgeable team of engineers visited the customer to understand the component. They studied the application and its problems practically, on the machine. Once done with the primary research, the customer asked for a tool drawing before beginning the trials of our reamers. The engineers provided the drawings to the customer and upon approval, started working on the trial tools. But between providing the drawings and getting the approval, we made several rounds of changes. These were based on the evolving data from the customer.
After preparation of the reamer body, when we were brazing the cermet tips on the reamer blank, our principals in Switzerland informed us that they had developed a new edge preparation which gave a better finish on such applications. We expedited the import of those cermet tips to conduct a timely trial.
All the above measures lead to a win-win situation for both, the management (cost saving) as well as the operators (effort reduced).
Check out our range of hole making products.