But we do not have more tooling stations on the machine”, was the last thing I heard that night. In 2019, one of our customers had “urgently” called me to automate the deburring process of their crankshaft cross holes. After 3 days of day and night trials, we solved the application successfully. Later, the customer bought 4 sets of deburring tools for their various lines only to realize later that they had ordered new machines which did not have stations.
This is just one of the many situations that I have encountered when working at client shop floors to solve their various machining applications. “The machine builder only gives warranty with a particular brand of grinding wheels” is one more issue. Yet another one is that higher parameters are unavailable on the machine. I was in Maharashtra to help a customer reduce cycle time on machining Inconel718 on a milling VMC. The customer spent 3 hours preparing the program for using a solid ceramic endmill. Later we realized, the maximum available speed on the machine was less than the speed required.
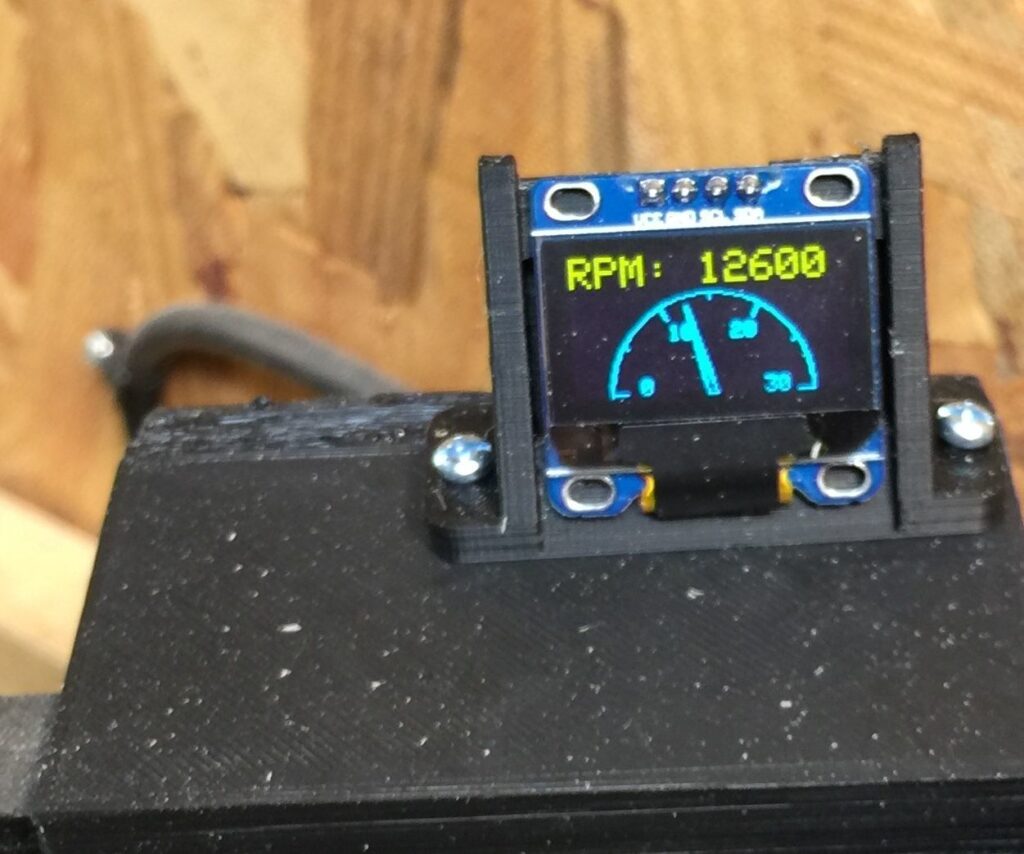
Before you buy a machine
So, I decided to write this article after having encountered such problems with CNC machines numerous times. Almost all the customers have such issues. Even the biggest OEMs too face one or more of these problems limiting their capability to produced faster and better. While you make a decision on which machine to buy, always keep the following points in mind:
Speeds and Feeds
Always keep the possibility of increasing your machining parameters open. Technology is always changing. For example, one of our partners is working on a new material that would machine steel two-times faster than CBN. Also, your volumes might shoot up forcing you to make a hasty purchase of a new machine unless your existing one can at least partly handle the load. The machine hour rate can very quickly eat up on all your profitability.
Sufficient Tooling Stations
The number of tool stations on your machines often limits your capability to make complex components. Initially, people ignore operations like deburring which is one of the most underestimated cot saver. Later, when the volumes go up, they struggle with high rejection rates. It is true that any number of station is never enough and we have to settle with something. I have a solution for this towards the end of this article.
Coolant Flow
It is widely known that people miss out on manufacturing capabilities if that machine cannot provide through-tool coolant. However, people often don’t know that even if the machine IS capable of supplying through-tool coolant, they might still miss on opportunities. Why? Because the coolant flow cannot be controlled by their CNC controller. A machine whose coolant pressure can be regulated using the CNC Controller has a lot of opportunities for low cost automation.
CNC Controller
We have often observed that the customers machines have a lot of capabilities that can optimize their machining operations. However, these are often locked. And after you have bought a machine and want to use one of those features, you need to buy a key from the manufacturer to “unlock” that feature. We have often observed this in clients having Swiss-style sliding head lathes. One of my clients in Bengaluru has 25 such machines by a popular Japanese machine maker. Most of them have Y-Axis capabilities leading to a much better chip-control. But all of them were locked and the client had to spend a good load of money to unlock those capabilities. However, at the time of machine purchase, the customer could have lucratively negotiated these.
Warranty
Machine builders often put clauses that limit your ability to use tooling from varied manufacturers. These clauses are mostly unfair trade practices and are usually illegal. But, oftentimes they end up making the machinist uptight about replacing the tooled up product with another one. Always ask your supplier to make all the clarification is writing. Also, double check these with other machine builders. If they are giving you the flexibility to use multiple suppliers, it is possible that the first machine builder is being unreasonable. Let the vendor know your concerns and you will find that the suppliers rigidity will start vanishing.
Consultation
Lastly, always consult your tooling, lubricants and fixturing suppliers before making the decision to buy a machine. By virtue of their wide range of customers, it is possible that they might have seen that machine before and can guide you with its pros and cons. Also, they can let you know about the latest cutting technology which might change your requirements. Some suppliers do it for free, some charge you a small amount. In my opinion, it is always preferable to pay up once than to pay up every day in the form of manufacturing costs.
I would like to conclude with the fact that it is not always possible to include all the above features in the same machine and make unaffordable. However, you can always try to keep your machines highly scalable. A machine that can be extended at a later time by adding different modules to it would be a better fit. Definitely more so than the one with a rigid configuration.